Whether it be dams or roads, buildings or data centers, concrete is ubiquitous in its presence as a construction material. It is the second-most used consumed material in the world after water. It is affordable, versatile and durable, all highly desirable properties. In 2020, production of concrete exceeded 14 billion cubic meters, a market that is only set to grow as our infrastructure demands increase due to the industrialization of the developing world.
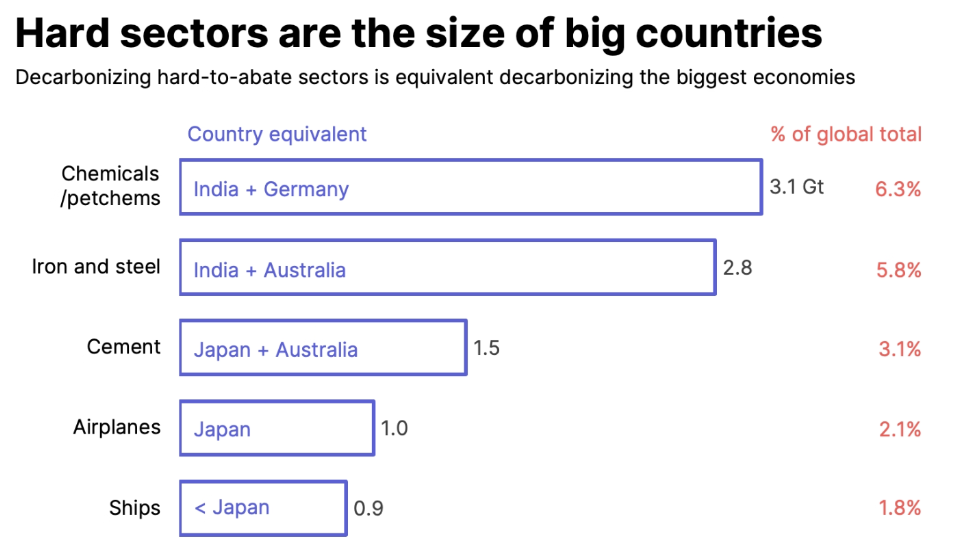
While development is certainly a good thing, focussing on sustainable development is the need of the hour. This cannot be more apparent than in the concrete and cement industry, which produces 8% of global CO2 emissions, more than any country except the US and China. We cannot halt progress: thus, the only option is to decarbonize the concrete industry itself.
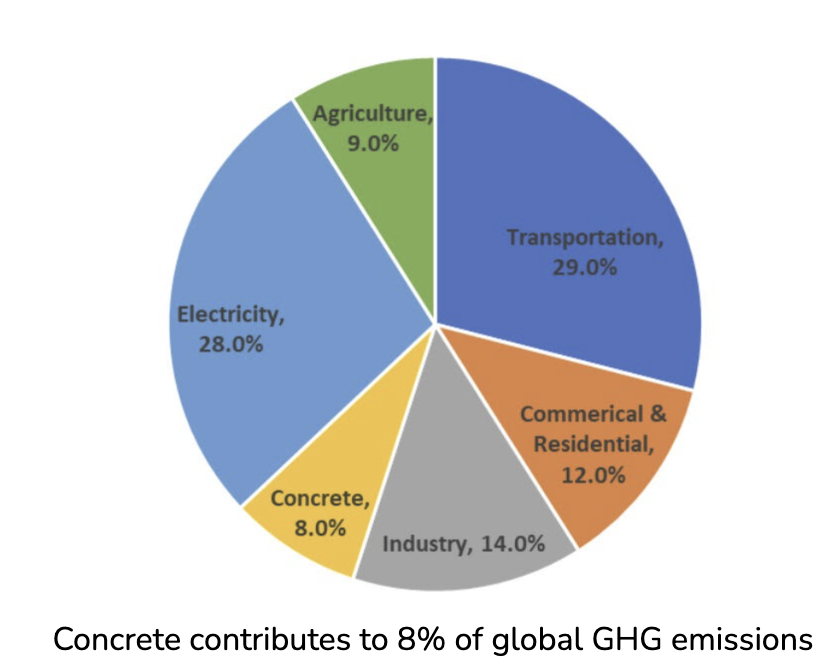
Concrete consists of approximately an 80-20 ratio of aggregates (e.g. sand) and cement paste. Despite this, cement makes up a vast majority of the GHG emissions of concrete as seen below
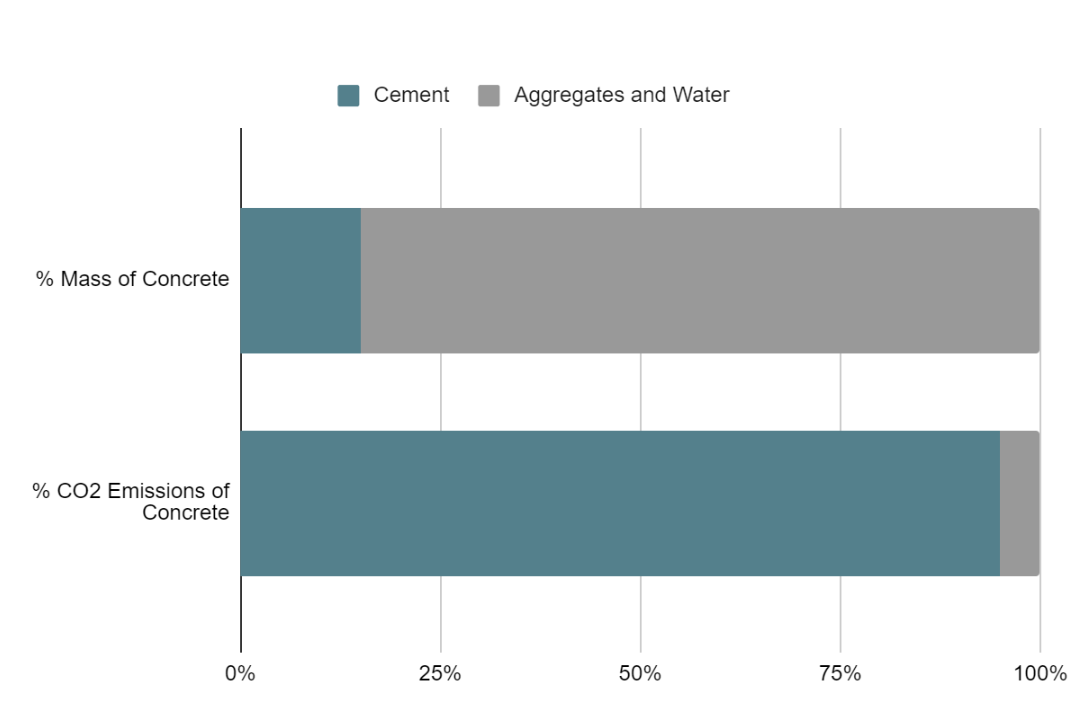
Emissions in the cement production process come from three main sources:
- Electricity: Electricity is utilized throughout the cement production plant; it is a vital component of any industry. Emissions from electricity will be automatically decarbonized as green energy takes over the grid.
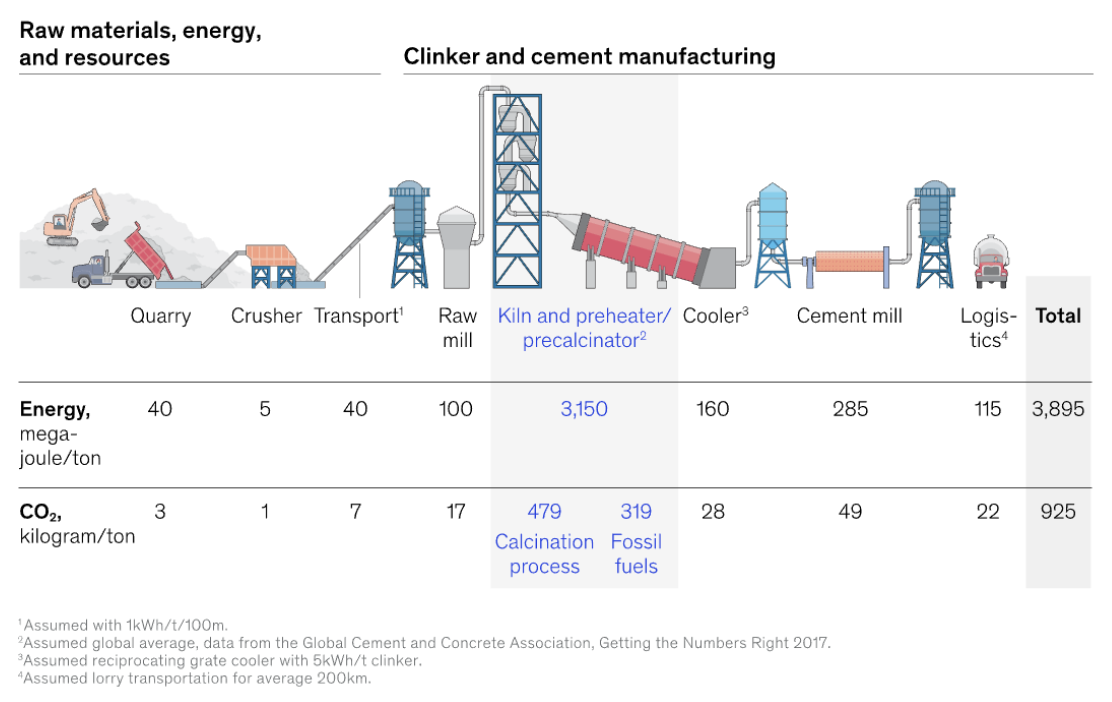
- Coal: The kiln is the main step in the cement production process. In it, limestone and clay/sand are heated to temperatures around 1500°C to form complex silicates. Coal is burned to achieve these temperatures. Decarbonisation of the rotary kiln goes hand in hand with efficient and safe electrical heating.
- Materials: Limestone is one of the main components of cement, making up ~40% of the clinker mass. CO2 emissions are an intrinsic part of the usage of limestone in cement-making due to the below reaction:
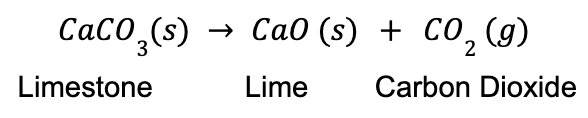
Technologies to decarbonize cement
For large corporations, the low-hanging fruit is process optimization: whether that be in the form of applying AI to redesign kilns for maximum efficiency, fixing inefficiencies in the production cycle, or using data analytics to reduce power consumption. While these are crucial, they are only stop-gap solutions to the larger goal of green cement.
Materials-based innovation in the space is crucial to eliminate the intrinsic emissions in cement production. Some solutions being explored include:
- Supplementary Cementitious Materials: SCMs refer to any waste product from other industries that can be mixed with cement to increase volume without impacting quality. HeildelbergMaterials is using SCMs such as fly ash to reduce cement CO2 emissions.
- LC3: Limestone Calcined Clay Cement uses low-grade clay as a replacement for limestone, greatly reducing emissions from cement. Ambuja Cement is involved in LC3 cement-making.
- Biocement: Biocement is a relatively new type of cement that uses biological materials to provide unique properties to cement such as the ability to self-heal. BioMason is a startup working in this space.
- Novel technologies: Many startups are working on novel solutions that may not be a direct change in cement composition. For example, CarbonCure and Solidia are both curing cement with CO2 instead of water, making it act as a carbon sink.
- Total replacement: Some companies such as Leko Labs are building materials that completely replace concrete in specific applications.
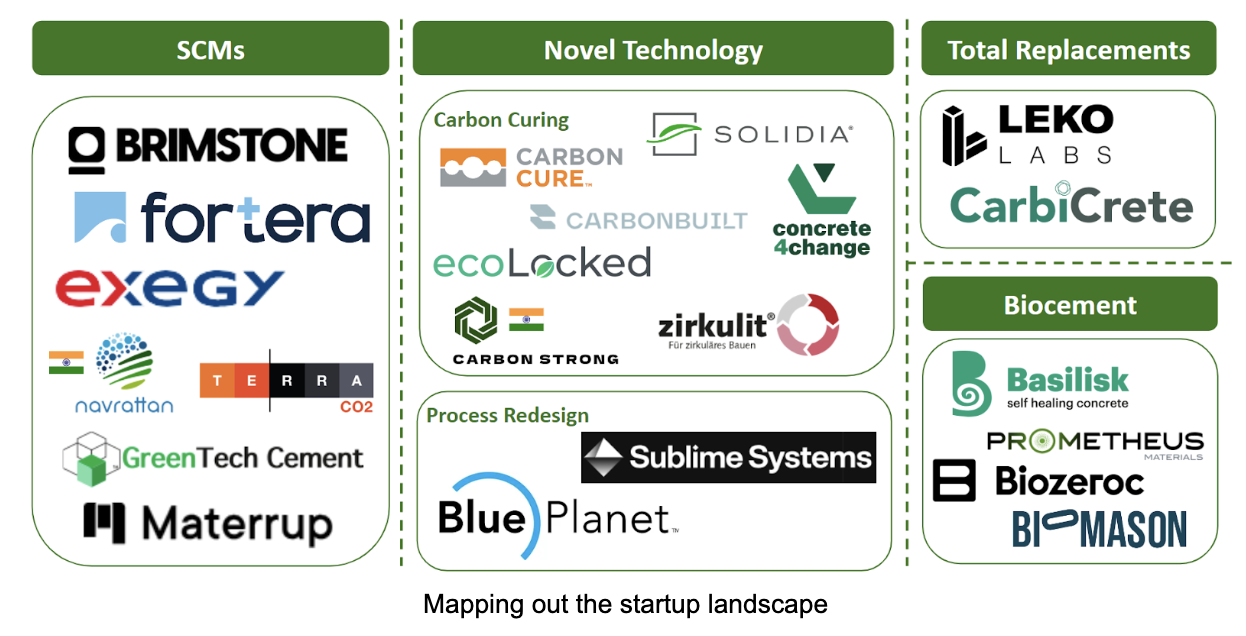
Aligning incentives
The Government of India has announced a plan to introduce a sector-wise green credit system (with infrastructure green credits being one of them) which will directly promote usage of green cement in construction. The Performance, Achieve, and Trade (PAT) scheme by the Ministry of Power provides incentives for cement manufacturers to reduce their energy consumption.
On the private sector side, The Green Pro certification by the CII provides numerous benefits in speeding up regulatory processes, and also helps in marketing. Sustainable buildings certified by IGBC have a variety of benefits depending on the state, including faster approvals and subsidies. As such, the cement industry has strong incentives to decarbonize.
The Cement Industry in India
Cement is a fairly regionally-fragmented industry, largely due to the high cost sensitivity of the market. Each manufacturer has a wide range of plants in many states to reduce transportation costs. As such, localized solutions to green cement is the model being followed by most companies. In India, 2 players control over half the market, with the top 8 covering 96%.
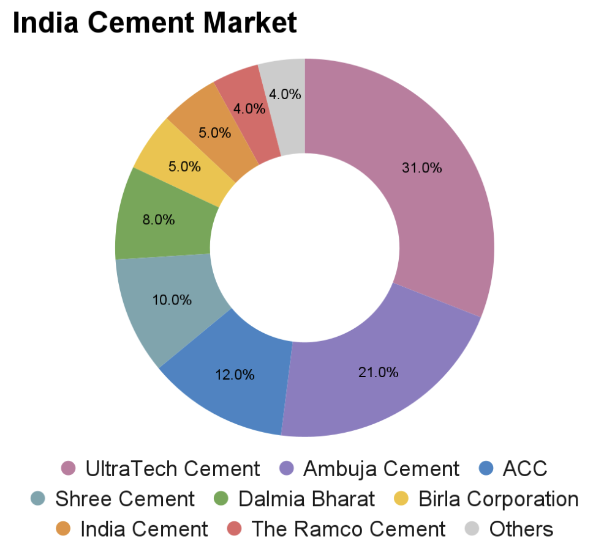
Many companies, both Indian and international, are making their move in the space:
- In January 2023, Adani’s ACC announced a new ECOMaxX product claiming to reduce up to 100% of CO2 emissions via binder substitution
- In May 2023, Ambuja Cement announced expansion of two green-energy-run cement facilities
- Heidelberg Materials has already launched a whole range of geography-specific solutions based on SCM supply
- Holcim has invested heavily in its new ECOPact product involving the use of SCMs and its own proprietary technology
A Huge Opportunity, but Difficult GTM
For a startup entering this space, the main opportunity lies in the sheer sector size, along with lack of out-of-the-box innovation. Most large players are using SCMs, which are limited in geography. It will also become difficult to rely on waste, especially as other industries move towards more sustainable processes that do not produce as much waste.
The rising demand of cement, In India – the largest importer of limestone in the world – great opportunity lies in technology that can reduce our limestone demand, especially with the push for internal manufacturing via Make in India.
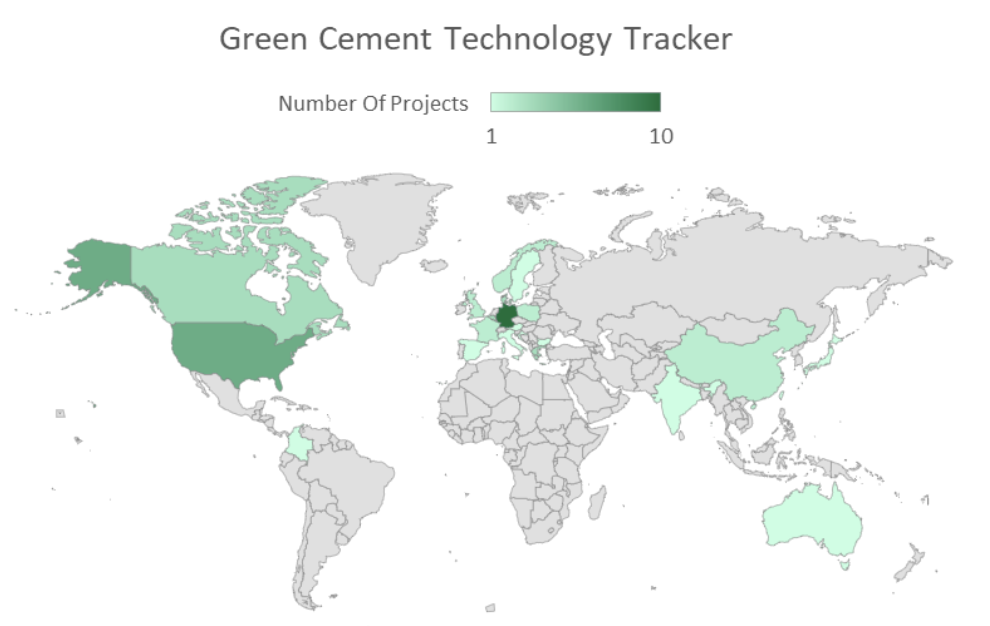
Conversely, the main risk lies in pricing and market adoption: due to the huge volumes cement is utilized in, the market is extremely price-sensitive. If the green cement product is more expensive, it needs to justify that price with significant value add during the construction phase itself. Builders have little brand loyalty, preferring the cheapest material that meets design specifications. Business development is an uphill battle.
Some overarching pointers to keep in mind -
- Cement manufacturing is a difficult business to grow in. A startup will be better off focussing on technology solutions that can be implemented in existing cement manufacturing plants/infrastructure projects.
- By providing a technology solution that existing players can implement in their processes, one can access a vast majority of the market upon converting just a few players.
- The more complicated and expensive the tech is, the harder it will be to sell.
- Scaling is a major factor in this market. The technology should be easy and economical to scale up.
- Operational innovation is as important as technological innovation in this space. Local value chains can be leveraged to create solutions that can be customized according to region.
The cement space is growing, and the need for decarbonization is critical. As a founder, there are several schemes and initiatives that will make the startup journey smoother. If you are building in the green cement or sustainable construction spaces, we would love to hear from you and learn from your experiences. Please write to us at sunil.cavale@specialeinvest.com.
We would like to thank, Atharva Jadhav, previously VC Fellow at Speciale Invest, who helped put this piece together.
We at Speciale Invest believe in supporting breakthrough technologies that have the potential to solve pressing global problems. As early stage investors, we like to get our hands dirty early on and support founders in their zero to one journey with patient capital, business development opportunities and hiring. We enjoy and thrive on the risk that comes with backing deep-tech startups at the pre-product stage and help through product-market fit, early customers and scale-up. To know more about Speciale’s investments in disruptive technologies, please check our portfolio